Every day around the world in hospitals and clinics, research laboratories and universities, numerous plastic products are used for medical parts, appliances and support equipment. The variety of applications is almost limitless.
This is due to the fact that plastic injection molding is perfect for making high volumes of identical, close-tolerance products. That includes both solid parts as well as hollow and semi-hollow enclosures and cases. And not only is it versatile, but also many plastic resins have demonstrated their utility in a variety of products that have already received regulatory approval. That means it will be relatively easier to get certification for new products using the same raw material.
To learn more about why it might be right for you, here are the top 4 reasons to consider plastic injection molding for making medical products.
1. Process Control and Reliability
The history of plastic injection molding goes back almost 100 years. That means the process has been continuously refined and improved to the point where it’s very stable and reliable. There is advanced modeling software available that takes much of the guesswork out of tool design. And, with modern digital controls on plastic injection molding machines, the process parameters can be quickly tuned for optimal performance and to reduce production lead time to a minimum.
2. High Volumes
All injection molding projects first start with a molding tool and die. To make a complex shape might require making an equally complex mold tool, so there is an initial product development investment that needs to be considered before a single part is made.
But once the tool is approved it’s possible to make hundreds of thousands of duplicate parts in plastic very quickly and economically. In fact, larger volumes tend to recoup the tooling costs over time because of lower price-per-part. This is perfect for rather generic items like containers, tubes or disposable single-use products like syringes.
3. Ideal for Enclosures
Injection molding is especially useful when making cases and enclosures. It’s technically possible to use some other process to make a box, such as CNC machining or vacuum casting, and sometimes there are good reasons for doing so. But those other methods would be much slower, consume more raw material, and would be prohibitively expensive. That why this would make sense only for low-volume or custom jobs when you don’t want to invest in a tool.
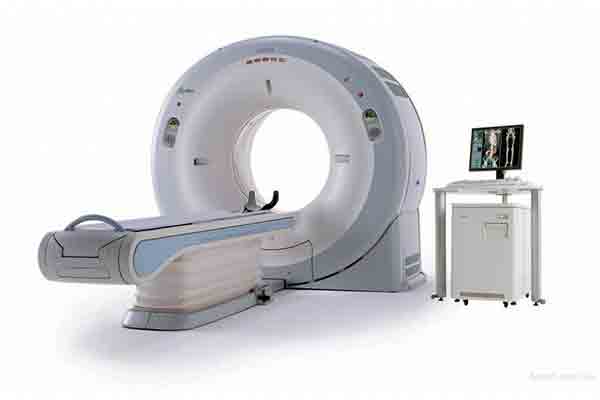
GE Optima CAT scan
Enclosures come in all shapes and sizes. Some are just simple parts like tool holding trays, pill dispensers or housings for sensors. Large plastic housings are especially beneficial for sophisticated medical equipment. Not only is plastic lightweight, durable and less expensive than an alternative material, it also will not interfere with electromagnetic energy such as would be used in CAT scans, MRIs and x-rays. And some plastics resins are also unaffected by radiation.
4. Versatility
There are thousands of plastic resins to choose from that are easily available on the commercial market. And luckily many of these resins are suitable for medical applications. These resins have mechanical and chemical properties which are well understood so it’s easy to choose the one that’s most appropriate for its end use and environment. There are resins that are heat stable, chemically resistant, strong, lightweight, biodegradable, and biocompatible. Plastic is increasingly popular when used for prosthetics, replacement joints or other products that will be in permanent contact with the body.
Want to learn more?
Michigan CNC Machining Parts, Inc. is fully certified to the quality management system of ISO 13485 for medical devices. When you’re ready to start your next medical product, contact us for a free design for manufacturing review and quotation. We can ensure you use the right material and the right process that best suits your application.
Chris Williams is the Content Editor at Michigan CNC Machining Parts, Inc.. He is passionate about writing and about developments in science, manufacturing and related technologies. He is also a certified English grammar snob.