Additive manufacturing in metal or plastic has some limitations as a high-volume production method. It does not, and maybe never will, compete with conventional manufacturing like plastic injection molding or CNC machining when it comes to ultimate speed and efficiency.
But that’s ok, because 3D printing is a perfect solution for quickly making models and end-use parts in support of healthcare and medical applications. The design flexibility and wide range of substrates means that more options are available than ever before to make highly customized parts. Here we take a closer look at the five major advantages of 3D printing for medical devices.
1. Digital Manufacturing and Design Flexibility
3D printed parts begin their life as digital three-dimensional CAD files in a computer program. Such designs can be created directly on a computer using readily available software, or they can be derived from a topological 3D scan of an actual physical object.
In either case, there are enormous advantages for the designer who can then easily manipulate and modify this shape in virtual space without needing to first create a physical sample. This saves development time and cost while improving the resulting finished product.
Such design freedom is especially important when dealing with the human body in all its complexity, where its often necessary to customize a generic part to suit the unique anatomy of a single user. Making modifications like these are fast and easy to do when there is no hard tooling involved.
2. 3D Mapping and Prototyping
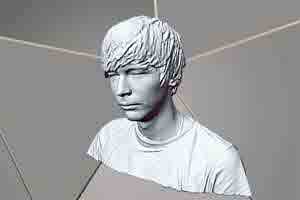
Courtesy of Artec3D
3D scanning technology, such as with advanced CT/ MRI, can be used to make highly accurate and detailed virtual models of human organs or bones. These can then be rendered as physical prototypes or models using a 3D printer. With such a model, doctors can then study and diagnose various conditions without needing to perform dangerous or intrusive surgery.
Models can then be used to help doctors plan out ideal surgical procedures in advance. This decreases the amount of time a patient is in the operating theater, which reduces riskwhile improving the chances for a positive outcome.
3. Decentralized Production
Unlike mass production processes, 3D printing does not need the industrial infrastructure of a large factory and a complex supply chain. Rather, small printers are truly desktop portable and can be used almost anywhere with electricity and a computer.
Because of this portability, it’s more common now to have 3D plastic printers on-site in hospitals and medical clinics. They can also be taken out into the field in remote areas that may not have access to any healthcare facilities. This means that medical technicians or bioengineers can fabricate some simple parts or prosthetics on the spot in emergency situations where and when they’re needed.
4. Optimized Engineering
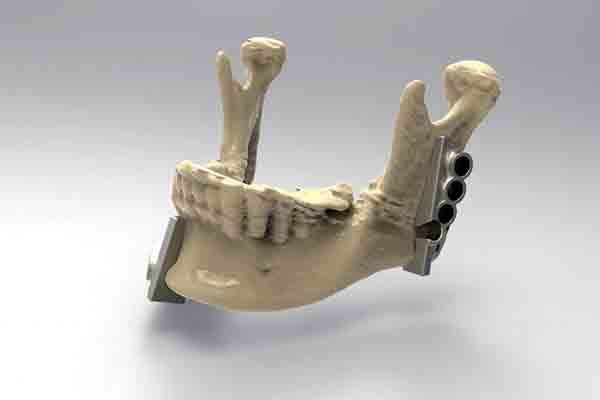
Surgical cutting guide. Courtesy of Renishaw
There are now many different technologies employed by 3D printers to make plastic and metal parts. They use a wide variety of substrates that have many unique chemical and mechanical properties.
Because of this, finished parts can be designed with varying characteristics that can be optimized for the final application. They can be flexible or rigid, soft and pliable or ultra-strong. Some parts are single-use and disposable while others can become permanent bone or joint replacements. And many of the newer printing technologies also allow two or more print media to be fused together into a single assembly, thereby combining several desirable attributes at once.
Furthermore, parts can be made with lightweight lattice structures that offer maximum strength with minimum weight. Such lattices are difficult if not impossible to make conventionally.
5. Speed and Volume Flexibility
Finally, 3D printing in metal or plastic is not limited by the same economies of scale that effect conventional manufacturing. There is no need to make specialized tooling, jigs or fixtures, and there are no minimum volume requirements or batch production limitations. As long as the design is ready, a single part can be made at the touch of a button. This kind of volume flexibility is especially desirable in emergency or remote situations where there is little or no infrastructure available to support batch orders and where a single much-needed item is a matter of life or death.
Want to learn more?
Michigan CNC Machining Parts, Inc. offers advanced metal 3D printing as well as expert technical advice and design support. Find out how we can support your next-generation medical product designs when you upload your CAD files for a free quotation and design review.
Chris Williams is the Content Editor at Michigan CNC Machining Parts, Inc.. He is passionate about writing and about developments in science, manufacturing and related technologies. He is also a certified English grammar snob.