Countless products today, from smartphones to supersonic jets, are made possible because of the reliability and versatility of CNC milling. It’s an ideal method for rapid prototyping, as well as volume manufacturing in plastic and metal. Let’s take a closer look at some of the advantages and applications for this remarkable machine tool.
What is CNC milling?
CNC milling is a manufacturing process that uses a cutting tool mounted on a rotating spindle to selectively remove material from a block of raw substrate. The workpiece is rigidly mounted to a table, and this table moves or rotates on different planes so the tool can work at many angles. Sophisticated machines can have 5 or more axes of independent motion for advanced applications.
What are Axes of Motion?
The axis of motion for a CNC mill depends on an X-Y-Z coordinate measuring system. All machinists refer to this when describing the basic movements of the mill, relative to an operator facing the machine. A standard CNC mill for example has three axes. The spindle represents the Z-axis, moving up and down. The X-axis is left-to-right, and the Y-axis is front-to-back.
Rotary tables can be added to CNC machines to provide additional movements, while 5-axis machines already have rotating work tables built-in.
What are the Advantages of Computer Numeric Control?
All of these movements rely on Computer Numeric Control, which is a computer program derived from a 3D digital file of the desired finished part.
Early automated machine tools relied on punch cards to control their basic movements in a systematic fashion. It worked but it was a slow and cumbersome system and punch cards could not be modified once made. These were later replaced by magnetic tapes, disk drives and now fully digital instructions in G-Code.
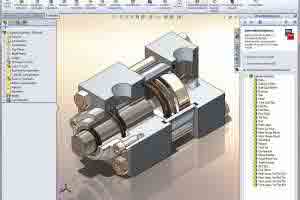
Image courtesy of Solidworks
This control system is not only fast and accurate but, unlike earlier systems, it can be easily modified as needed, line-by-line and in real time, in order to fine-tune the program for the best results.
What are the Benefits of Automatic Tool Changing?
Making a finished part from a block of material requires many different tools, each of them performing a very specific machining function. Changing these tools one at a time by hand would be prohibitively time-consuming and inefficient.
To counter this, CNC mills have rotating carousels where all the needed tools are pre-loaded on separate holders. When needed, these tools can be exchanged automatically on the spindle within a few seconds.
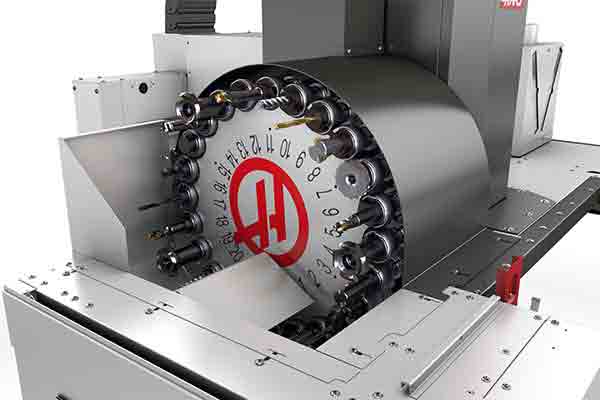
Haas VF-2SS tool holding carousel
The carousel on this Haas VF-2SS mill can hold a maximum of 30 tools, plus one on the spindle. This guarantees that all conventional milling operations can be performed in one set-up. We further improve on this efficiency by using an automated tool dispensing system from Guhring. With more than ten thousand cutters in storage we are always assured of having the right tool for every job.
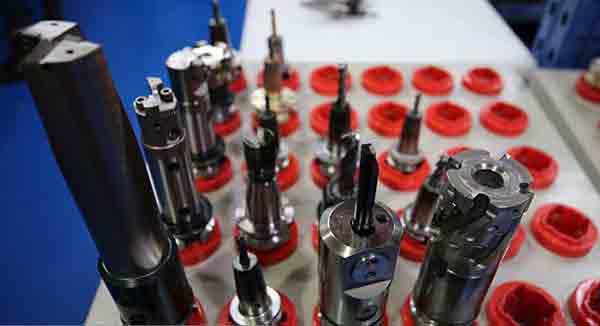
A variety of pre-mounted cutting tools
The Importance of Workpiece Holding
On a CNC mill the workpiece is mounted in a fixed position on a work table while the tool is moved around it. This is the fundamental difference from turning, where the workpiece spins while the tool remains stationary.
Because of this fundamental difference in motion, parts are held in place in very different ways on these two machines. In CNC turning, for example, all parts are mounted on a spindle. They are concentric and therefore held securely by a three-jaw chuck right down the centerline of the part, the same way every time. The same is not true for CNC milling, where different holding strategies are needed.
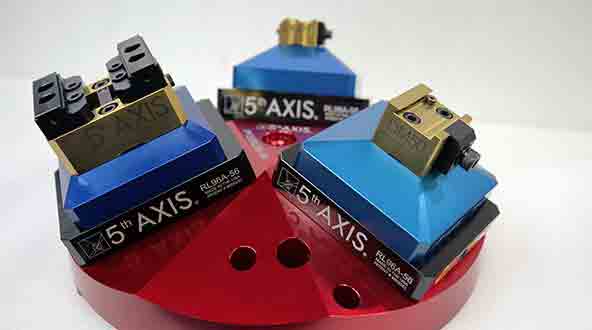
5-axis tool mounting system
Simple rectangular shapes are easy to hold in place, either by being mounted in a machinist’s vice or clamped directly to the table’s surface.
However, other unusual shapes may require custom holding fixtures which can make a project more complex and time consuming. We have designed several of our own which were later patented.
How Does CNC Milling Help You Get Great Parts?
Symmetrical parts that are essentially round or radial are best machined on a CNC turning center for maximum efficiency. But most parts we work with are not round or symmetrical so they must be machined on a mill.
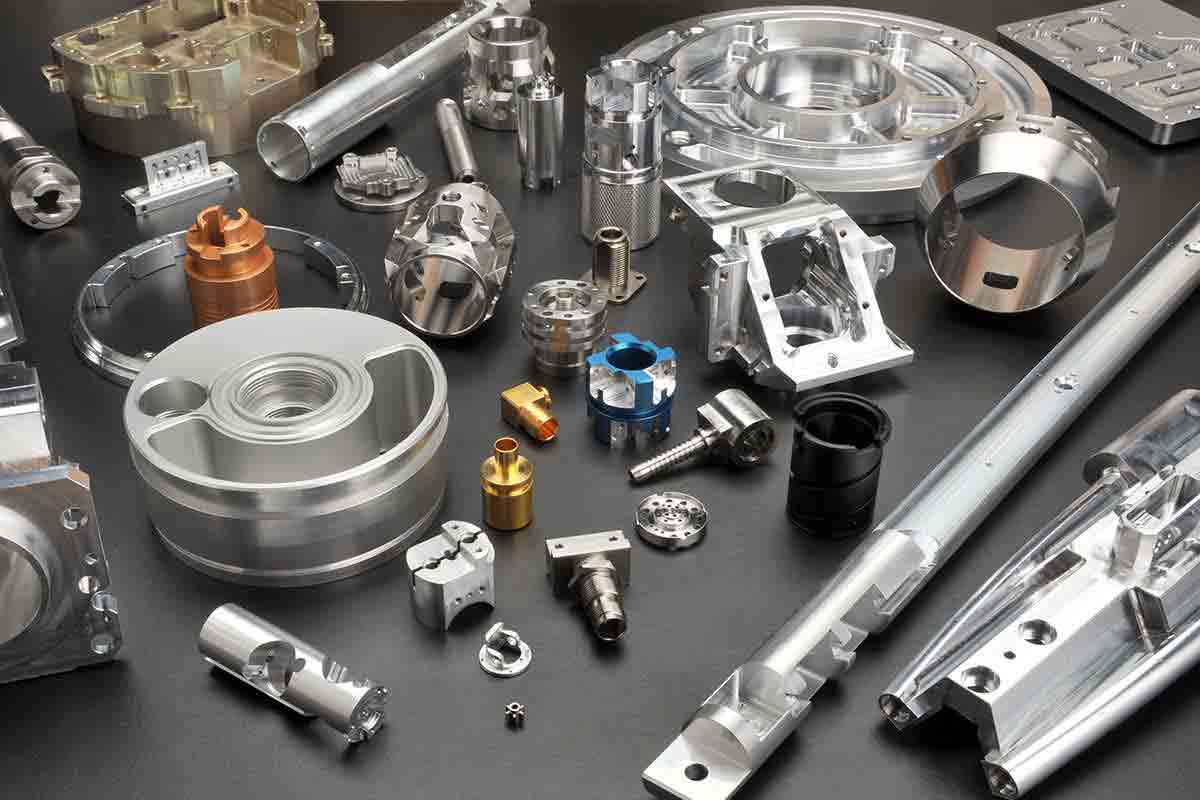
Image courtesy of evden.com
Multi-axis mills are unrivalled for creating square shapes, bevels, angles, slots and complex curves – any subtractive machining process can be done on a mill, including making round shapes. They are also accurate, routinely holding tolerances of .01mm or 10 microns. We have a wide variety of stock materials for any application and offer the best incoming material inspection and testing service.
When you upload your CAD files to Michigan CNC Machining Parts, Inc. for a free quotation, not only will you get great parts and prototypes fast, you get peace of mind.
Chris Williams is the Content Editor at Michigan CNC Machining Parts, Inc.. He is passionate about writing and about developments in science, manufacturing and related technologies. He is also a certified English grammar snob.