A Walkthrough of the Aluminum Anodizing and Color Matching Process
Anodizing is a great way to put an attractive and physically durable finish on aluminum parts. Anodizing improves corrosion resistance, surface hardness, prevents scratching and is an ideal foundation for painting, glue or powder coating.
There are many challenges when trying to match colors on anodized parts. Some of these challenges come from the process itself, and some are a result of the metal alloy being used.
Product developers need to know about the key factors that affect color consistency and color matching in Type II anodizing for aluminum, which is the most common type of anodizing found on everyday products.
Cleaning and Etching
Anodizing starts with cleaning the part in a series of detergent and rinsing tanks.
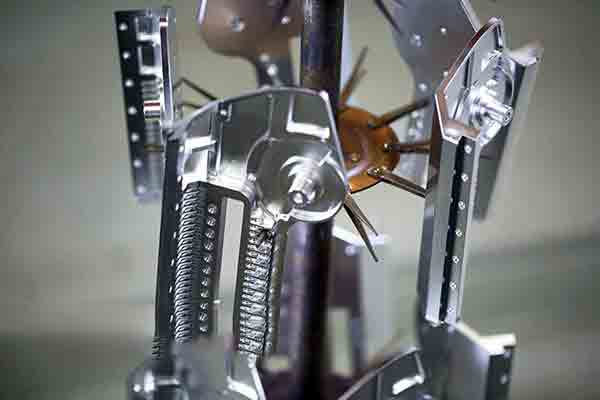
Parts being washed before anodizing
Both etching and brightening remove trace amounts of metal. This alters the surface chemistry of the piece at the molecular level. The amount of material removed is based on many conditions including temperature, time, solution Ph, and the size and shape of the part. So this first process creates some variability in the finished product that is hard to control precisely.
Building the Film Layer
After cleaning, the next step is to build up a layer of aluminum oxide. The part is suspended in a tank of sulfuric acid (the electrolyte), and an electric current is used to produce micro-pores in the surface of the target part. The size and shape of the pores depends on the metal alloy. These pores get filled with free oxygen ions in the electrolyte to create a strong yet porous oxide layer.
The depth of the pores depends on tank temperature, solution concentration, time in the tank and most especially electric voltage. More time in the tank and/or higher power will produce deeper pores, meaning a thicker film of aluminum oxide will be formed. This is very hard to control exactly since pore depth cannot be actively measured during anodizing and can only be estimated based on general conditions.
Metallurgy
The single biggest factor affecting color is the constituency of the base metal. The presence of trace elements like zinc, copper, manganese and silicon are essential for the performance of the alloy. But these elements don’t respond to the anodizing process in the same way and again lead to unpredictable color variations.
Adding Color
There are two ways to add color to aluminum during anodizing. One way is electrolytic coloring. The part is immersed in yet another tank of solution, along with metallic salts. These salts fill in the pores and make a very strong coating that resists UV fading, but these colors are usually limited to a bronze or black color.
The second method is dip coloring, or simply placing the part in a tank of dye. The dye is absorbed into the pores, and then the surface is boiled in de-ionized water to halt any further reactions. There are many color choices with this method, but the colors may not be very UV resistant so they can fade over time.
The Result
The final visual appearance is not only formed by the color of the dye but also by the depth of the pores. This affects how light is absorbed or reflected off the surface. As mentioned, different elements in the alloy affect the size and shape of pores and the absorption of dyes.
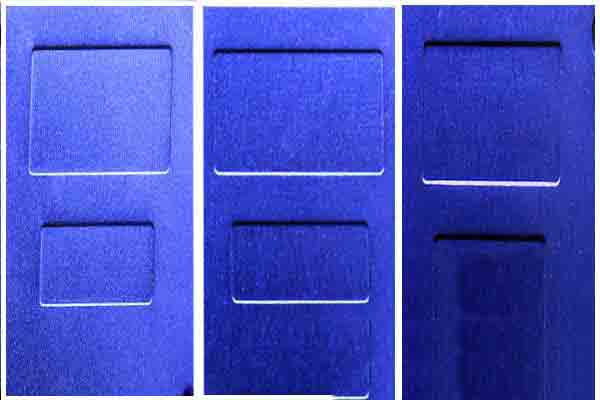
Color variations in anodized parts
All of these complex interactions make it impractical to expect an anodized finish that exactly matches a color swatch or sample. Rather, product developers should anticipate an allowable range of deviation from a target value. Further, deviation is possible from one lot to another, even under tightly controlled conditions.
Finally, it should be noted that not all colors can be reproduced on all substrates. For the best results, contact us in advance to discuss your color requirements and we can offer advice based on the metal alloy and the final application. Learn more when you upload your CAD files for a free quotation today.
Chris Williams is the Content Editor at Michigan CNC Machining Parts, Inc.. He is passionate about writing and about developments in science, manufacturing and related technologies. He is also a certified English grammar snob.